Ultrasonic welding for diapers
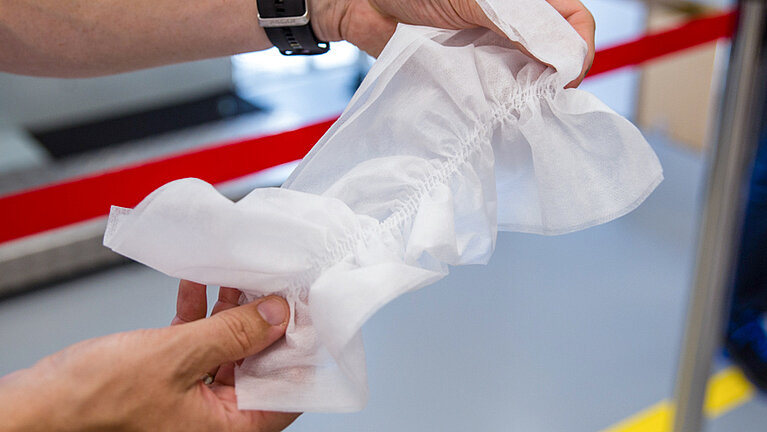
Our solution for elastic cuffs
By means of the ultrasonic process, multilayer absorbent bodies, e.g. a diaper, including the SAP granules (Super Absorbent Polymer) can be welded glue-free and in one single step. Now Herrmann Ultraschall offers an innovative process for elastic cuffs.
The elastic threads that act as leak protection on the leg cut-out provide the comfort that consumers want. Inserting the elastic threads is a difficult process that Herrmann Ultraschall is now introducing an ultrasonic fixing solution for. The elastic thread is attached in precisely the right position, regardless of the diaper format, by means of a rotating sonotrode and a controlled generator signal. The process does not involve the use of adhesive or other additives and does not impair the thread’s functional properties.
The new process is made possible by further developments in the ULTRABOND ultrasonic generator, which “triggers” the ultrasonics in the right places, instead of using a continous sonic process. The generator regulates the weld tool movement (amplitude) extremely quickly, ensuring an almost free configuration of the intermittent weld result. The thread is trapped in a “tunnel”, produced in the nonwovens by welding, and remains permanently embedded. Multi-dimensional process monitoring results from combining this with the MICROGAP gap control, which is the monitoring of the distance between the material and weld tool.
Format-dependent tools are no longer needed, because the areas to be welded can be freely configured using an analog signal, rendering a format anvil drum unnecessary. This reduces setup times and production costs. The fact that the anvil drum can be used for different diaper sizes makes life easier for diaper manufacturers. Based on results from current fundamental research in the ultrasonic laboratory, Herrmann will recommend specific anvil engravings for this application in the future.
-
Interview with our Head of Applications Development
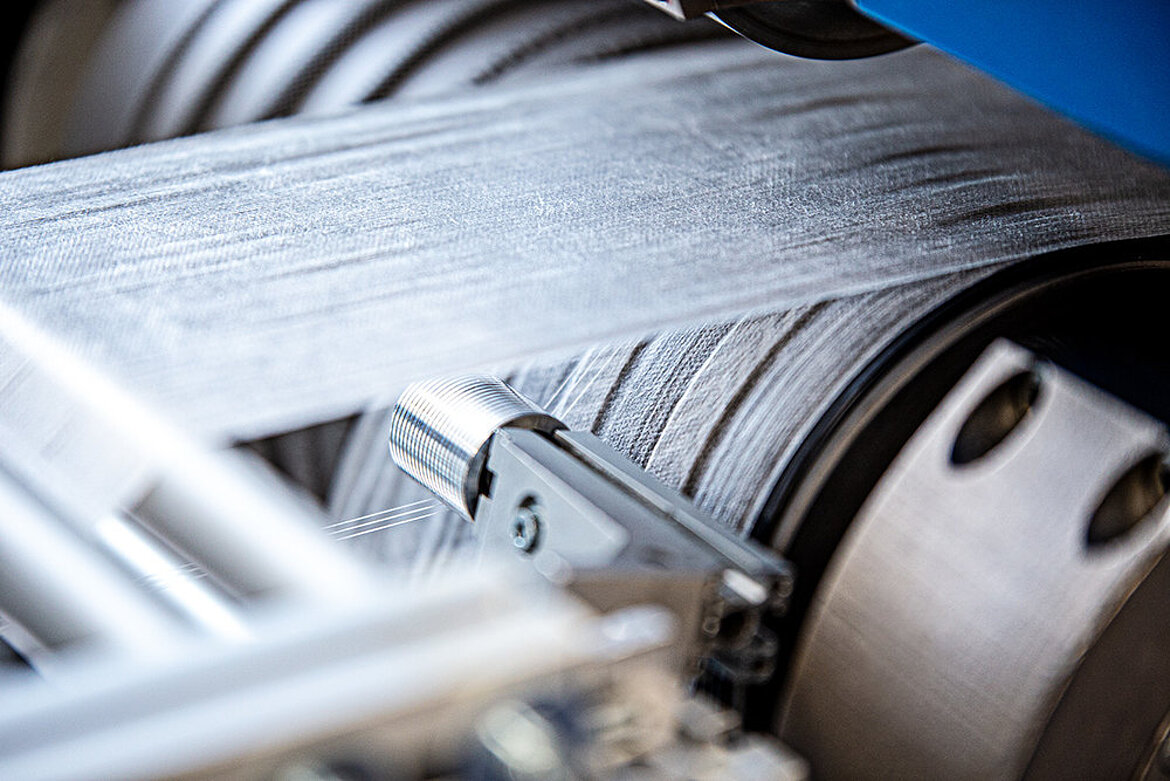